La programmation PLC présente plusieurs pièges classiques, même pour les ingénieurs expérimentés. Voici un tour d’horizon des erreurs courantes en programmation PLC, accompagnées de stratégies pratiques pour les éviter efficacement.
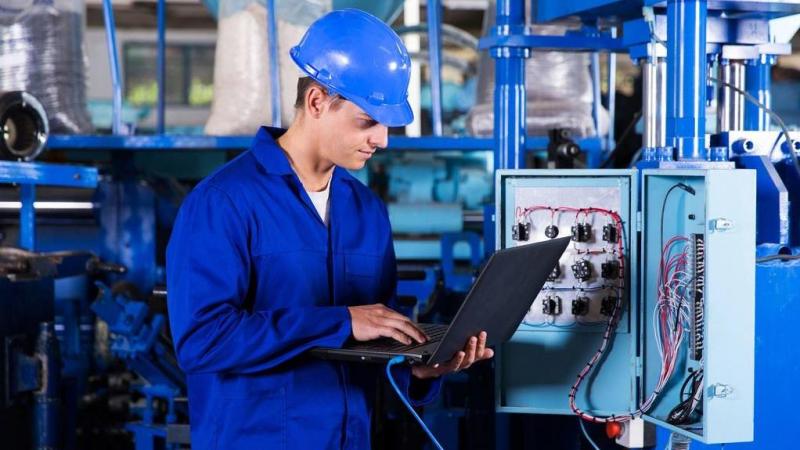
Erreurs logiques
Sorties à bobine double
Erreur fréquente : Affecter plusieurs fois la même bobine de sortie dans le programme provoque des comportements imprévisibles.
Solution : Vérifiez attentivement la logique de programmation pour que chaque sortie PLC ne soit affectée qu’une seule fois.
Flux logique mal défini
Erreur fréquente : Une logique confuse entraîne des séquences de contrôle incorrectes.
Solution : Optez pour une programmation structurée, comme les diagrammes d’état ou diagrammes de flux, pour clarifier le déroulement du programme.
Erreurs de type de données et conversions
Types de données incompatibles
Erreur fréquente : Mélanger des types de données mal adaptés peut générer des erreurs de calcul.
Solution : Uniformisez vos types de variables PLC et effectuez les conversions de données de manière explicite.
Comparaison directe de flottants
Erreur fréquente : Comparer des nombres à virgule flottante sans tolérance génère des erreurs de précision.
Solution : Utilisez une marge de tolérance pour les comparaisons au lieu de rechercher une égalité exacte.
Erreurs de minuterie et de compteur
Mauvaise réinitialisation des temporisateurs
Erreur fréquente : Oublier de réinitialiser les minuteries et compteurs peut empêcher leur bon fonctionnement.
Solution : Réinitialisez-les à des moments logiques pour maintenir une fonctionnalité PLC précise.
Impulsions trop brèves
Erreur fréquente : Des signaux d’entrée trop courts ne déclenchent pas la minuterie.
Solution : Assurez-vous que la durée du signal est suffisante ou utilisez des déclenchements par front.
Problèmes de communication PLC
Mauvais paramètres de communication
Erreur fréquente : Des paramètres de communication PLC mal définis bloquent l’échange avec les périphériques.
Solution : Vérifiez les vitesses en bauds, bits de données, parité et adresses IP PLC.
Timeouts non gérés
Erreur fréquente : Les délais de communication mal gérés provoquent des blocages ou erreurs d’exécution.
Solution : Prévoyez des délais raisonnables et implémentez une gestion d’erreur de communication fiable.
Absence de gestion des erreurs
Pannes non détectées
Erreur fréquente : Ignorer les conditions d’erreur, comme les défauts d’entrée ou de périphériques, rend le système instable.
Solution : Intégrez une gestion d’erreurs automatisée, avec alertes et diagnostics.
Interruptions mal gérées
Erreur fréquente : Une gestion confuse des interruptions PLC ralentit les réactions du système.
Solution : Créez une logique d’interruption claire et testez les priorités d’exécution.
Manque de maintenabilité du programme
Absence de commentaires
Erreur fréquente : Un code PLC sans commentaires devient difficile à maintenir.
Solution : Rédigez une documentation claire, avec des commentaires ligne par ligne expliquant chaque étape.
Redondance excessive
Erreur fréquente : Trop de code dupliqué nuit à la lisibilité et à la mise à jour.
Solution : Utilisez des blocs de fonctions pour factoriser le code et le rendre évolutif.
Erreurs de configuration matérielle
Mauvais paramétrage I/O
Erreur fréquente : Une configuration I/O incorrecte engendre des erreurs de lecture ou de commande.
Solution : Vérifiez que chaque module I/O a l’adresse correcte et le type de signal approprié.
Erreurs de câblage
Erreur fréquente : Un câblage mal réalisé peut causer des dommages matériels ou un dysfonctionnement.
Solution : Respectez les schémas électriques, testez les liaisons et utilisez des outils de diagnostic.
Conclusion : maîtrisez votre programmation PLC
Éviter ces erreurs de programmation PLC est essentiel pour garantir la fiabilité, la performance et la durabilité de vos systèmes d’automatisation industrielle. En adoptant ces bonnes pratiques, vous améliorez considérablement la qualité de vos projets PLC, que ce soit avec des automates Siemens, Schneider, ou d’autres marques.